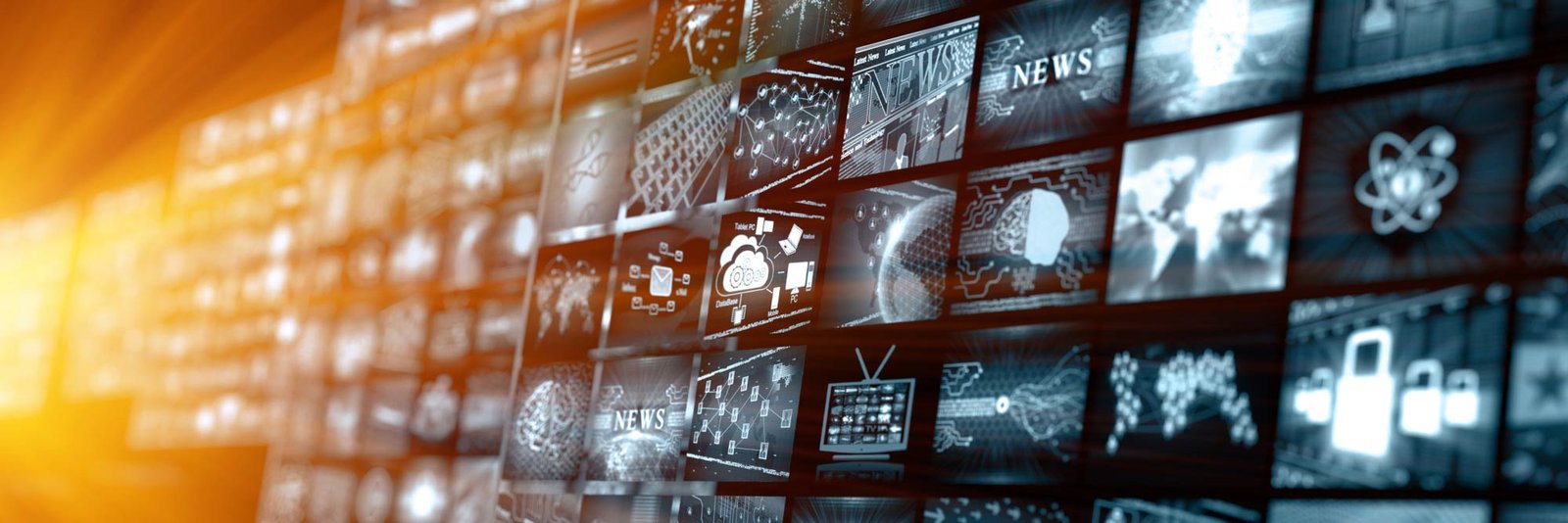
Articles

Forklifts are indispensable machines for transporting and lifting a wide variety of materials in manufacturing, warehousing and construction environments. Also, their versatile design makes them useful for tasks ranging from basic horizontal transportation to elevated storage and retrieval.
Forklift truck design and operation:
The basic design of a forklift consists of a powered chassis with an operator cabin, two front-mounted lifting forks and a rear mounted power unit with battery or fuel tank. Also, electric and internal combustion-powered models are common.
Operators control forklift motion through a steering column and use foot pedals to lift/lower forks or drive forward/backward. Additional levers typically control fork functions like tilting, sideshifting or attachment operations. Outriggers or stabilizers provide stability when lifting loads.
Main forklift truck types:
Sit-down counterbalance: Most common type with the operator seated and counterweights behind the forks for stability during lifting.
Reach trucks: Extended forks can raise loads as high as 22 ft for multi-tier product retrieval and storage.
Swing-Reach: Combines 360-degree rotation and vertical forks reaching racks and shelves on multiple sides.
Rough terrain: Heavier-duty versions handle outdoor conditions with larger tires and rugged frames.
Electric: Battery-powered models suitable for indoor use where emissions aren’t a concern.
Forklift training Safety:
Safety is paramount due to forklifts’ large loads and operation in cluttered areas around pedestrians. Also, operators must complete forklift certification which involves hands-on testing of skills like load handling, stability control and hazard avoidance maneuvers.
Additionally, forklift inspection and maintenance programs keep brakes, tires, mast components and alarms functioning properly to avoid accidents from equipment malfunctions. Conspicuous markings make forklifts visible in low light.
Agria forklift Applications:
Material handling ranges from transporting full pallets to picking individual cases. Common uses include:
- Warehousing: Picking, packing and staging product in distribution facilities.
- Manufacturing: Moving parts/subassemblies between assembly lines and inventory areas.
- Construction: Transporting building supplies around job sites for storage and rise to upper levels.
- Ports/freight: Loading/unloading intermodal containers and truck trailers.
- Retail: Assisting with deliveries into stores and restocking inventory.
- Agriculture: Storing and transporting fertilizer, grain and other bulk commodities.
Forklift training manufacturers and models:
Leading global brands include Toyota (8-Series), Jungheinrich (VFG), Crown (SC), Hyster (H8-50FT), and Nissan/Raymond (Raymond R30TT).
Common electric models are Agria FE for smaller spaces and Byd Li-Ion Reach for taller racking. Larger internal combustion forklifts include the 10,000-pound capacity Hyster H360FT.
CNC machines for metalworking enhancing efficiency and safety with forklifts:
Lifting capacity:
Ranges from 2,000 to over 36,000 lbs. depending on class and manufacturer. Higher capacities need commercial driver’s license.
Attachments:
Forks, platforms, clamps and scoops enable different load handling tasks. Also, rotating forks and side shifters improve positioning.
Fuel/power:
Liquid propane or diesel internal combustion engines remain common outdoors. Electric models use lead-acid or lithium-ion batteries.
Drive motors:
AC drive motors in electric forklifts provide more power and longer run times than DC. Also, internal combustion uses hydraulic pumps.
Forks: Standard 48″ steel forks can lift loads up to 4 feet high. Also, narrower forks or extendable forks reach farther or lift higher.
Operator area:
Enclosed cabs provide visibility and protection from elements. Also, seat belts and rollover protection are required safety features.
Tires and wheels:
Pneumatic tires in various sizes up to 17.5″ diameter. Dual front wheels improve traction in rough conditions.
Rental options:
Renting forklifts short-term from equipment dealers handles temporary workload increases or seasonal demands.
Technologies:
Collision avoidance systems, telematics monitoring also, automated guided vehicles expand forklift applications.
Safety Features:
Forklift in the metalworking industry are equipped with a range of safety features to protect operators and prevent accidents. These features include overhead guards to shield operators from falling objects, audible alarms to alert nearby personnel, visibility enhancements such as rearview mirrors and cameras, and lights for improved visibility in low-light conditions. Additionally, some forklift models have advanced safety systems, such as automatic braking or speed limiters, to minimize the risk of collisions and promote safe operation.
Load Capacity Monitoring:
Some modern forklifts are equipped with load capacity monitoring systems. Also, these systems use sensors and technology to measure the weight of the load being lifted and provide real-time feedback to the operator. Load capacity monitoring helps prevent overloading, which can lead to stability issues and accidents. Also, it enables operators to make informed decisions and ensures that loads are handled within safe limits.
Maintenance and Servicing:
Regular maintenance and servicing are crucial for the optimal performance and longevity of forklifts in metalworking operations. Scheduled maintenance includes tasks such as checking fluid levels, inspecting brakes and tires, lubricating moving parts, and conducting overall system checks. Also, adhering to maintenance schedules and promptly addressing any issues or repairs helps prevent breakdowns, ensures safe operation, and extends the lifespan of the forklifts.
Training and Certification:
Adequate training and certification for forklift operators are essential to promote safe and efficient operations in the metalworking industry. Also, operators should receive comprehensive training on forklift operation, load handling techniques, maneuvering in different environments, and safety procedures. Certification programs ensure that operators have the necessary knowledge and skills to operate forklifts safely. Also, ongoing training and refresher courses should be provided to keep operators up to date with best practices and safety standards.
Ergonomics and Operator Comfort:
Forklift manufacturers prioritize operator comfort and ergonomics to reduce fatigue, enhance productivity, and minimize the risk of musculoskeletal disorders. Also, features such as adjustable seats, ergonomic controls, and well-designed operator compartments contribute to a comfortable working environment. Additionally, vibration dampening technology, reduced noise levels, and ergonomic pedal placement help reduce operator fatigue during long shifts.
Integration with Warehouse Management Systems:
Forklift can be integrated with warehouse management systems (WMS) to streamline operations and improve efficiency. Also, integration allows for real-time communication between forklifts and the WMS, enabling accurate inventory tracking, optimizing material flow, and facilitating efficient picking and storage processes. This integration minimizes errors, enhances inventory management, and increases overall operational efficiency.
Environmental Considerations:
Environmental sustainability is a growing concern in the metalworking industry. Forklift manufacturers are increasingly focusing on developing environmentally friendly models. Also, electric forklifts, in particular, contribute to reduced carbon emissions and noise pollution. They eliminate the need for fossil fuels, leading to cleaner operations and improved air quality within the workspace.
Telematics and Data Analytics:
Telematics technology is being utilized in forklifts to gather and analyze data related to their performance, usage patterns, and maintenance needs. Also, this data can be used to optimize fleet management, track equipment utilization, plan maintenance schedules, and identify areas for operational improvement. Telematics systems provide valuable insights into forklift operations, enabling businesses to make data-driven decisions and improve overall efficiency.
Industry Regulations and Standards:
Forklift in the metalworking industry must adhere to specific regulations and standards to ensure safety and compliance. These regulations may vary depending on the region or country. Also, it is essential for businesses to stay updated with relevant safety standards and comply with regulations related to forklift operation, maintenance, and operator training.
By considering these aspects and leveraging the capabilities of forklifts, businesses in the metalworking industry can optimize their operations, improve safety, and achieve higher levels of productivity and efficiency. Forklift play a crucial role in material handling, ensuring the smooth flow of materials and contributing to the overall success of metalworking operations.