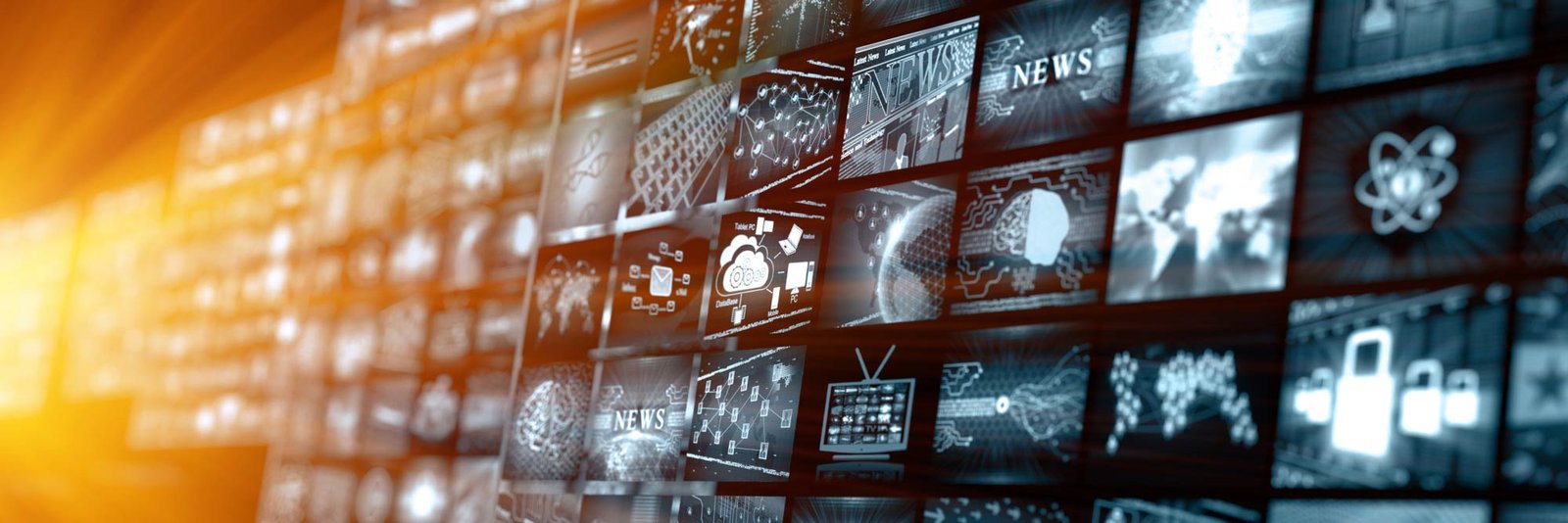
Articles
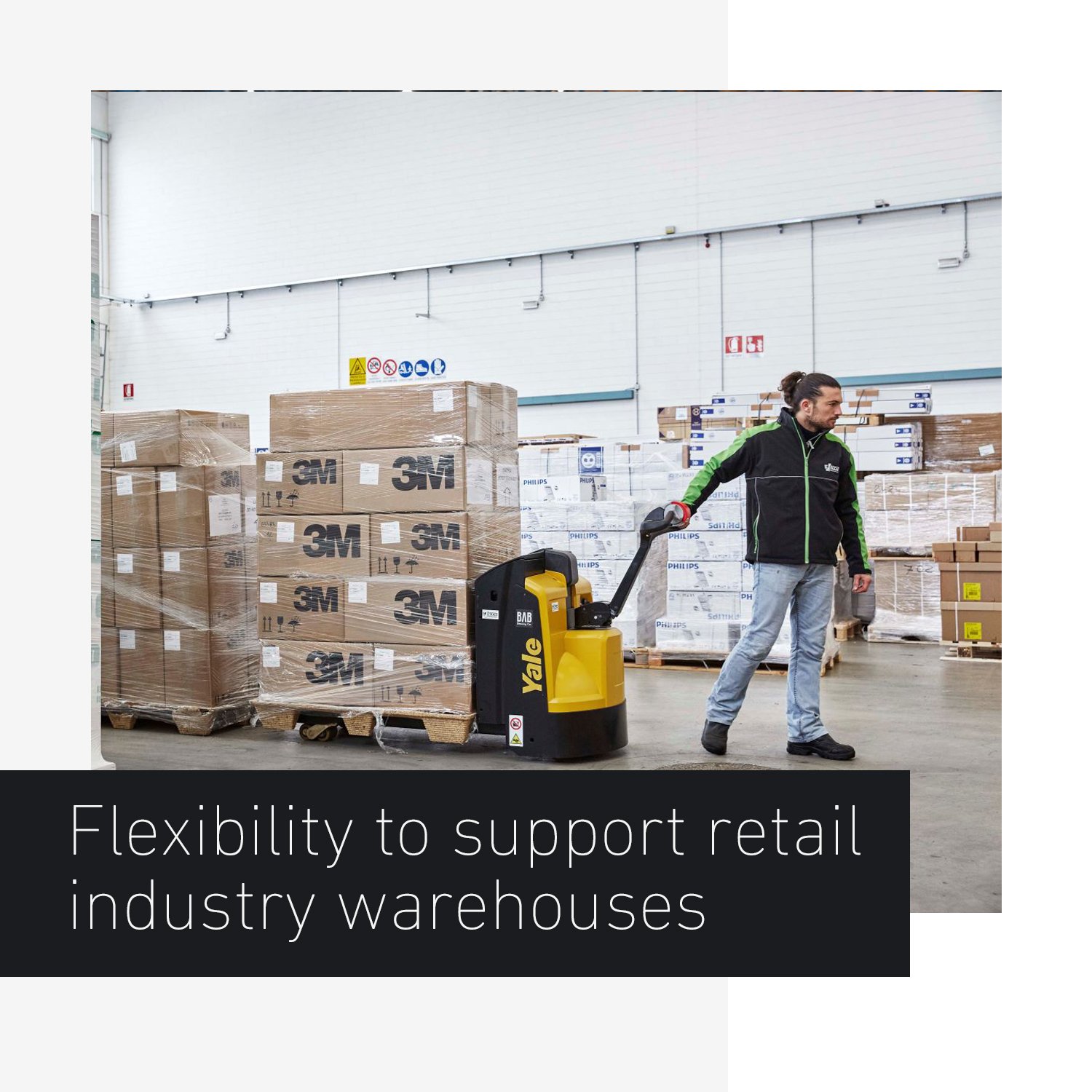
material handling equipment is crucial for businesses across industries. This article explores the importance of material handling, highlights key considerations for selecting appropriate equipment, provides best practices for optimizing processes, and examines trends in the field. By focusing on material handling efficiency, businesses can improve productivity, reduce costs, and enhance workplace safety.
Types of Material Handling Equipment:
This section provides an overview of common material handling equipment, including forklifts, conveyors, pallet jacks, automated guided vehicles (AGVs), and robotic systems. It explains the purpose, features, and benefits of each type, helping readers understand which equipment aligns with their specific needs. Materials handling encompasses a wide range of tools, vehicles, and machinery designed to facilitate the movement, storage, control, and protection of materials and products. Here is a paragraph highlighting various types of material handling equipment:
One of the crucial components of efficient material handling is the utilization of appropriate equipment. Forklifts are versatile machines used for lifting and carrying heavy loads, while reach trucks are designed for narrow aisle applications. Electric pallet jacks and hand pallet trucks are ideal for moving loads on pallets. Conveyor systems, such as belt conveyors and roller conveyors, are used to transport materials smoothly and efficiently within a facility. Automated guided vehicles (AGVs) and automated guided carts (AGCs) are self-propelled vehicles that navigate predetermined paths to transport materials. Palletizers and depalletizers automate the process of stacking and unstacking pallets. Lift tables and scissor lifts provide vertical lifting capabilities for ergonomic and efficient material positioning.
Choosing the Right Material Handling Equipment:
Selecting suitable materials handling involves evaluating factors such as material type and weight, facility layout, operational requirements, and safety considerations. By providing guidance on assessing different options, readers gain insights into choosing the most appropriate equipment for their applications.
When selecting material handling equipment, it is essential to consider several factors to ensure the right choice for your specific needs. Factors such as the type and weight of materials, facility layout, operational requirements, and safety considerations should be carefully evaluated. By assessing these factors, businesses can choose equipment that aligns with their requirements, optimizes material handling processes, and enhances overall efficiency.
Best Practices:
This section shares practical best practices for efficient and safe material handling. Topics covered include proper training for equipment operators, regular maintenance and inspections, effective inventory management, and optimizing workflow and layout design. Real-life examples and tips are provided to help readers implement these practices in their own operations.
Implementing best practices in material handling is crucial for optimizing efficiency, reducing costs, and ensuring workplace safety. First and foremost, proper training and certification for equipment operators is essential. Operators should be well-versed in equipment operation, safety protocols, and load-handling techniques. Regular equipment maintenance and inspections are also vital to prevent breakdowns and ensure optimal performance. Efficient inventory management, including accurate tracking and labeling systems, helps streamline material flow and reduces errors.
Additionally, optimizing workflow and layout design can minimize unnecessary movement and maximize productivity. Employing ergonomic principles, such as providing proper lifting equipment and training, reduces the risk of injuries and promotes employee well-being. Lastly, fostering a safety culture through ongoing training, clear communication, and regular safety audits creates a proactive environment where employees prioritize safety in all material handling activities. By implementing these best practices, businesses can enhance their material handling processes and achieve greater operational efficiency and workplace safety.
Automation and Technology:
Automation and technology play a pivotal role in revolutionizing material handling processes. One key aspect is the integration of warehouse management systems (WMS), which enable real-time monitoring, inventory tracking, and order fulfillment. These systems provide accurate data and insights, allowing businesses to make informed decisions and optimize their operations. Furthermore, barcode scanning and radio-frequency identification (RFID) technology streamline material identification and tracking, reducing errors and enhancing overall efficiency. Automated guided vehicles (AGVs) and robotic systems have also gained prominence, offering automated material transportation, sorting, and stacking capabilities.
These technologies eliminate manual labor, improve throughput, and enhance safety by reducing the risk of human error and accidents. Additionally, predictive maintenance systems leverage machine learning and data analytics to monitor equipment performance, enabling proactive maintenance to prevent breakdowns and costly downtime. By leveraging automation and technology in material handling, businesses can achieve higher productivity, accuracy, and cost savings, ultimately gaining a competitive edge in today’s fast-paced market.
Safety Considerations about material handling :
When it comes to material handling, safety should always be a top priority. Proper training and certification for equipment operators are essential to ensure they are equipped with the necessary skills and knowledge to operate machinery safely. Emphasizing the importance of following safety protocols, such as wearing personal protective equipment (PPE) and using proper lifting techniques, helps prevent accidents and injuries. Ergonomic considerations, such as providing adjustable workstations and equipment, help reduce strain and promote employee well-being. Regular safety audits and inspections identify potential hazards and enable proactive measures to mitigate risks. By prioritizing safety in material handling operations, businesses create a culture that values the well-being of employees and minimizes the potential for workplace accidents.
Case Studies:
One notable case study highlights the success of Company XYZ in improving its material handling processes. Facing challenges with manual order picking and limited warehouse space, they implemented an automated storage and retrieval system (AS/RS). The AS/RS utilized robotic technology to handle inventory, reducing the need for manual labor and increasing picking accuracy. This resulted in a significant reduction in errors and improved order fulfillment speed. The system also optimized space utilization, enabling the company to store more products within the same footprint. As a result, Company XYZ experienced a substantial increase in productivity and cost savings. The success of this case study demonstrates the transformative impact of implementing advanced material handling technologies, showcasing how businesses can achieve significant improvements in efficiency, accuracy, and overall operational performance.
Future Trends:
The future of materials handling is shaped by emerging trends and technologies. One such trend is the integration of artificial intelligence (AI) and machine learning, enabling systems to analyze data and make intelligent decisions in real time. This opens up possibilities for predictive analytics, optimizing routing and scheduling, and improving demand forecasting accuracy. Additionally, the Internet of Things (IoT) enables the connectivity of devices and sensors, providing real-time visibility and control over material handling processes. Autonomous mobile robots (AMRs) are gaining traction, offering flexibility and adaptability in navigating warehouse environments and performing various material handling tasks. The use of drones for inventory management and order fulfillment is also on the rise, promising faster and more efficient operations. As technology continues to advance, the future of material handling holds exciting opportunities for increased automation, connectivity, and optimization.
Conclusion:
The article concludes by summarizing the key points discussed. It emphasizes the significance of implementing efficient materials handling practices and encourages readers to assess their current processes, identify areas for improvement, and consider adopting new technologies and best practices. By prioritizing materials handling efficiency, businesses can unlock productivity gains, cost savings, and enhanced safety in their operations.