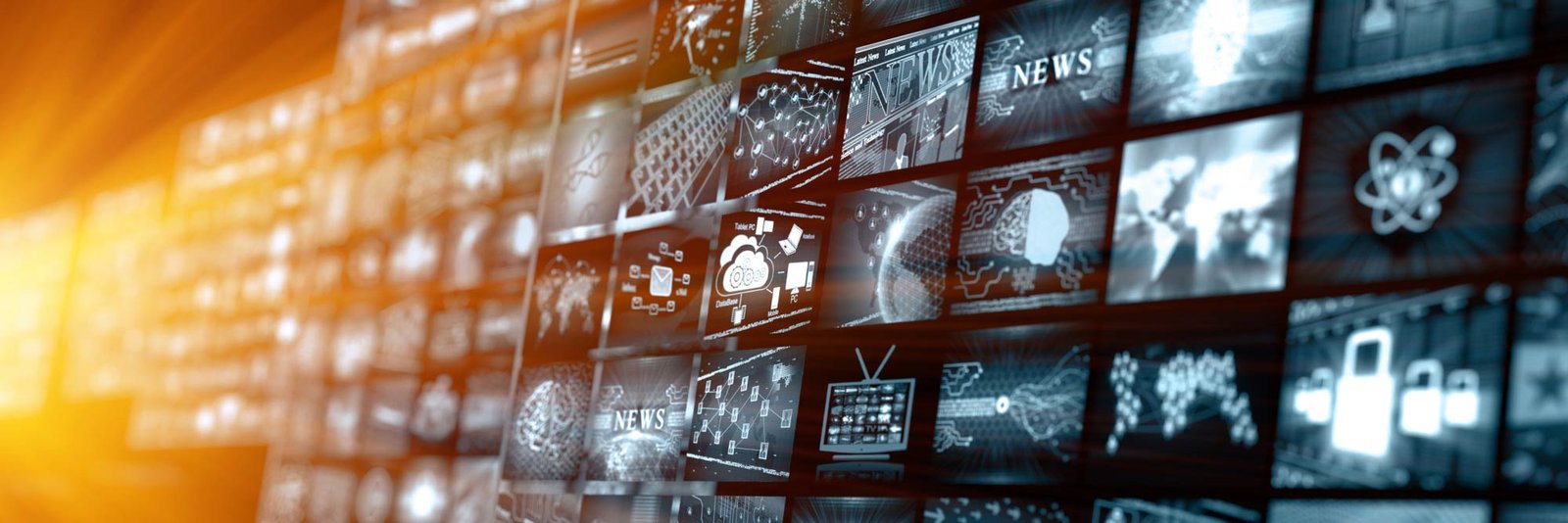
Articles
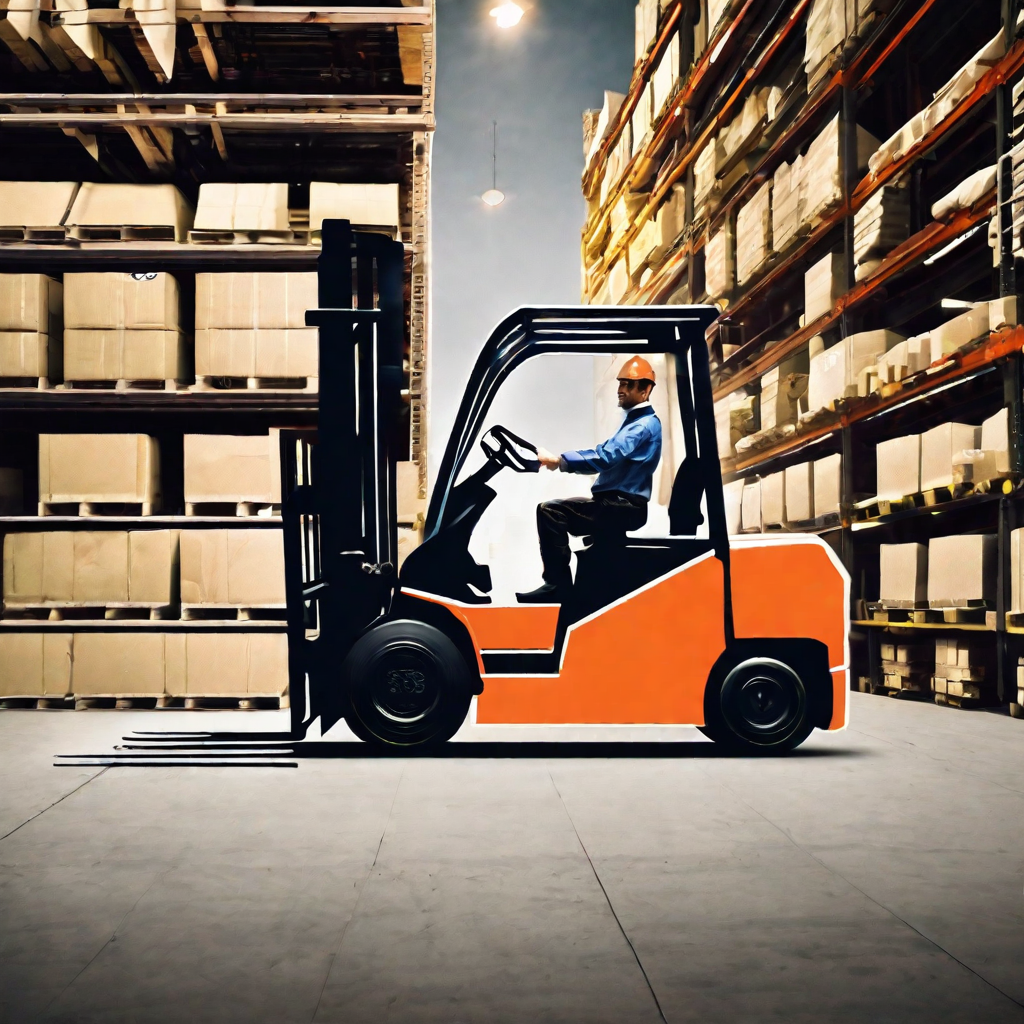
A forklift, also known as a lift truck or industrial truck, is a powerful and versatile machine widely used in warehouses, distribution centers, manufacturing facilities, and other material handling environments. Forklifts are designed to efficiently lift, transport, and stack various types of loads, making them essential equipment for moving heavy goods and materials. So, these vehicles are equipped with a pair of forks attached to the front that can be raised and lowered hydraulically to support and lift loads. Forklifts come in different sizes and capacities to accommodate varying load requirements, ranging from small electric forklifts used for light-duty tasks to large diesel-powered forklifts capable of handling heavy loads.
1. Understanding forklifts:
- Lifting and Carrying Capacity:
One of the primary functions of a forklift is its ability to lift heavy loads. Forklifts are equipped with hydraulic systems that use forks or attachments to raise and lower loads. They have a specified lifting capacity, which indicates the maximum weight they can safely lift. Forklifts are available in a range of load capacities, typically ranging from a few thousand pounds to over 50,000 pounds, depending on the type and model. - Power Sources:
- Electric forklifts, powered by rechargeable batteries, offer quiet operation, zero emissions, and lower maintenance requirements. They are suitable for indoor use and environments with limited ventilation. These forklifts provide higher power and faster acceleration, making them suitable for outdoor and heavy-duty applications. However, they produce emissions and require regular fueling or refilling.
2. Benefits of forklift companies:
Increased Productivity: Forklifts significantly enhance productivity in material handling tasks. Compared to manual handling methods, forklifts can lift and transport heavy loads much faster and with less effort. This efficiency allows for quicker completion of tasks such as loading and unloading trucks, stacking and retrieving materials, and moving items within a warehouse or storage facility.
Reduced Manual Labor: By employing forklifts, businesses can reduce the reliance on manual labor for physically demanding tasks. Forklifts eliminate the need for workers to manually carry heavy loads, reducing the risk of strain or injury. This frees human resources to focus on other value-added activities, improving overall operational efficiency.
Improved Safety: Forklifts are designed with safety features and operator training to minimize the risk of accidents. They provide better control and stability when handling loads, reducing the chances of dropping or damaging items. Additionally, forklifts come equipped with features like horns, lights, and mirrors to improve visibility and alert others in the vicinity. Proper training and adherence to safety protocols further ensure a safe working environment.
Efficient Use of Warehouse Space:
Forklifts enable efficient utilization of warehouse space. With their ability to stack and retrieve materials vertically, forklifts maximize vertical storage capacity. So, this allows businesses to optimize their warehouse layout and store more goods within a given footprint. By utilizing warehouse space effectively, businesses can reduce the need for larger facilities and associated costs.
Faster Loading and Unloading: Forklifts expedite the loading and unloading of goods, whether onto trucks, shelves, or storage racks. Forklifts can navigate tight spaces and reach elevated heights, making it easier to position items accurately. This speed and precision result in reduced waiting times for transport vehicles, faster order fulfillment, and improved customer satisfaction.
Streamlined Inventory Management: Forklifts contribute to efficient inventory management processes. They enable accurate and timely counting, sorting, and organizing of goods, reducing errors and improving inventory accuracy. Forklifts can quickly move items from one location to another, facilitating efficient stock rotation and minimizing the risk of obsolete or expired products.
3. Electric forklift Considerations:
- Operator Training and Certification: Proper training and certification of forklift operators are essential for safe operations. Operators should receive comprehensive training on forklift operation, including theoretical knowledge and practical skills. Training programs cover topics such as load handling, maneuvering in different environments, and safety procedures. Certification ensures that operators have demonstrated competence in operating forklifts safely.
- Adherence to Safety Regulations and Guidelines: Forklift operations are subject to safety regulations and guidelines set by regulatory bodies such as the Occupational Safety and Health Administration (OSHA) in the United States. Businesses must comply with these regulations, which include requirements for training, equipment maintenance, and safe operating practices. Adhering to these guidelines helps create a safety culture and reduces the risk of accidents.
- Regular Maintenance and Inspections: Proper maintenance and regular inspections of forklifts are vital for ensuring their safe operation. This includes routine checks of components such as brakes, tires, steering, and hydraulic systems. To prevent equipment failure and maintain optimal performance, it is important to follow scheduled maintenance procedures such as lubrication, filter changes, and battery maintenance (for electric forklifts).
-
Use of Safety Features:
Forklifts are equipped with various safety features, including seat belts, overhead guards, horns, lights, and mirrors, which should be utilized to enhance operator and pedestrian safety. Operators should receive effective and consistent training on the use of these safety features. Additionally, audible and visual warning devices, such as backup alarms and flashing lights, can alert pedestrians to the presence of a forklift in operation.
- Safe Operating Practices: Safe operating practices are essential for preventing accidents and injuries. Operators should follow guidelines such as:
- Observe speed limits and maintain appropriate speeds for different environments.
- Maintain a clear line of sight and be aware of the surroundings.
- Use designated travel paths and avoid congested areas when possible.
- Keep a safe distance from edges, ramps, and other potential hazards.
- Secure loads properly and ensure they are within the forklift’s weight capacity.
- Avoid sudden or jerky movements that can lead to instability or tip-overs
6. Reporting and Investigating Incidents: In the event of an accident, near-miss, or equipment malfunction, it is important to report and investigate the incident. So, this helps identify the root causes, implement corrective actions, and prevent similar incidents in the future. Establishing a reporting and investigation process fosters a culture of continuous improvement and safety awareness.
4. Types of Forklift truck:
Several types of forklifts are available, each designed for specific applications and environments. Some common types include:
- Counterbalance Forklifts: These are the most common type of forklifts, featuring a weight distribution system that allows them to carry loads in front of the mast without tipping over. Also, they are available in electric and IC variations.
- Reach Trucks: Reach trucks are designed for narrow aisle operations. They have extendable forks and a mast that can reach forward to pick up or deposit loads on high-racking systems.
- Order Pickers: Order pickers are used for manual order-picking tasks. Also, they feature an elevated platform that allows operators to access items at different heights without climbing up and down.
- Pallet Jacks: Pallet jacks, also known as pallet trucks, are used for horizontal transportation of palletized loads. They do not have a lifting mechanism but are manually or electrically operated.
5. Advances in Forklifts Technology:
Operator Training and Certification: Proper training and certification of forklift operators are essential for safe operations. Operators should receive comprehensive training on forklift operation, including theoretical knowledge and practical skills. Training programs cover topics such as load handling, maneuvering in different environments, and safety procedures. Certification ensures that operators have demonstrated competence in operating forklifts safely.
Adherence to Safety Regulations and Guidelines: Forklift operations are subject to safety regulations and guidelines set by regulatory bodies such as the Occupational Safety and Health Administration (OSHA) in the United States. Businesses must comply with these regulations, which include requirements for training, equipment maintenance, and safe operating practices. Adhering to these guidelines helps create a safety culture and reduces the risk of accidents.
Regular Maintenance and Inspections:
Proper maintenance and regular inspections of forklifts are vital for ensuring their safe operation. This includes routine checks of components such as brakes, tires, steering, and hydraulic systems. To prevent equipment failure and maintain optimal performance, it is important to follow scheduled maintenance procedures such as lubrication, filter changes, and battery maintenance (for electric forklifts).
Use of Safety Features: Forklifts are equipped with various safety features that should be utilized to enhance operator and pedestrian safety. These features include seat belts, overhead guards, horns, lights, and mirrors. Operators should be trained to use these safety features effectively and consistently. Additionally, audible and visual warning devices, such as backup alarms and flashing lights, can alert pedestrians to the presence of a forklift in operation.
Conclusion:
Forklifts have transformed material handling and warehouse operations, enabling efficient and safe movement of goods. Their versatility, functionalities, and benefits make them indispensable in various industries. By understanding the features, applications, safety considerations, and technological advancements associated with forklifts, businesses can leverage their capabilities to optimize warehouse productivity and enhance overall operational efficiency.