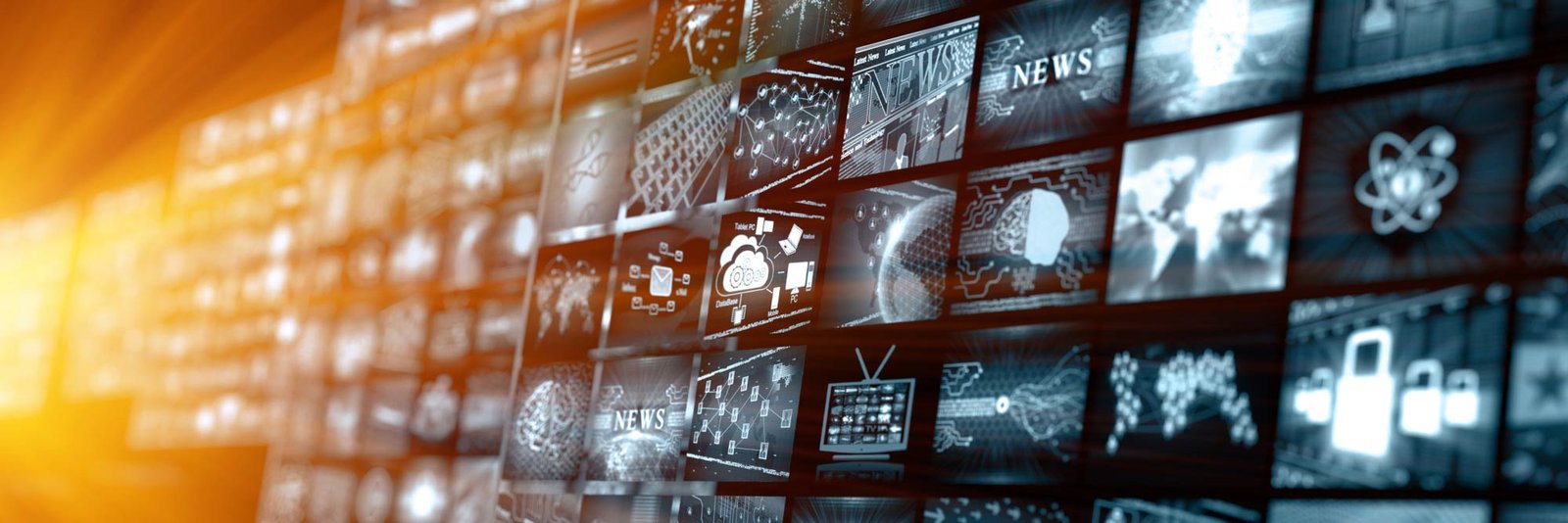
Articles
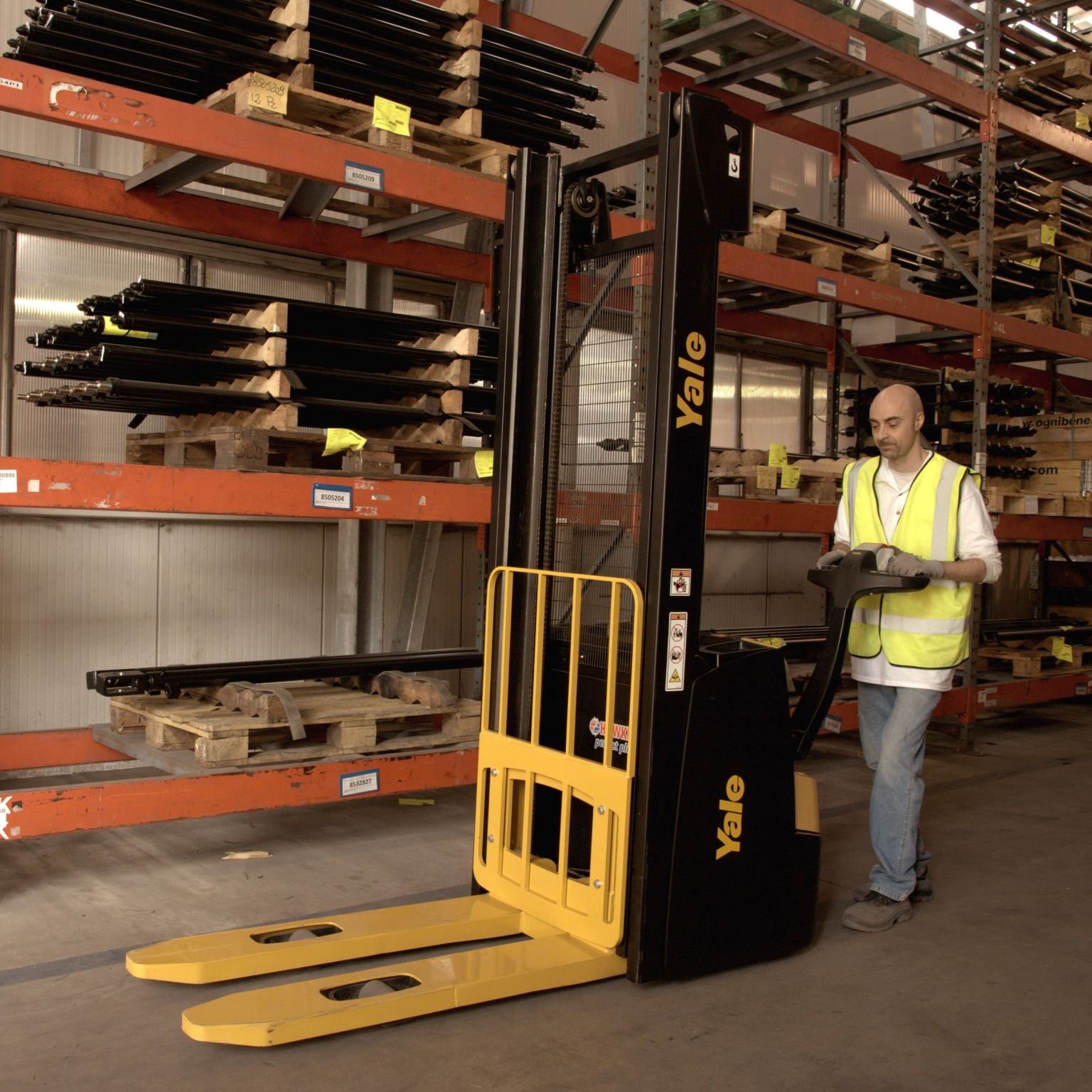
Material handling is the process of transporting goods, such as products and raw materials, within a warehouse or manufacturing facility or between a facility and a vehicle. It includes the transportation of these commodities and products and their storage, protection, and management.
Damaging any items throughout this process will impact your entire production. Therefore, it’s critical to maintain safe storage and handling conditions and efficient transportation techniques.
The Role of Material Handling in Warehouse Efficiency and Safety:
Material handling can move final products from factories. And distribute them to customers or sales outlets. Material handling equipment uses manual, semi-automatic, and automated machinery to transport and store materials inside the warehouse. Also, it can be used in various industries. material handling is most frequently in warehousing. where products must be safely recovered and shipped.
Material handling plays a critical role in optimizing warehouse efficiency and safety. It involves movement and storage.
This article will explore various material handling solutions and best practices to improve warehouse operations and ensure the safety of employees.
Types of Material Handling Equipment:
There are several types of material handling equipment designed to increase efficiency and safety in a warehouse environment. Some of the most common include:
- Forklifts: Forklifts are versatile vehicles used for lifting, moving, and stacking pallets or other heavy loads. They come in various designs, such as counterbalance forklifts, reach trucks, and order pickers, each with unique features and capabilities.
- Conveyors: Conveyor systems help move products and materials from one location to another within a warehouse, reducing manual handling and increasing efficiency. also, they can be powered or gravity-driven and come in different styles, such as belt conveyors, roller conveyors, or overhead conveyors.
- Pallet Racking: Pallet racking systems provide organized storage for palletized goods, maximizing warehouse space and improving inventory management. and they come in various configurations, such as selective, drive-in, push-back, and pallet flow racks.
- Automated Storage and Retrieval Systems (AS/RS): AS/RS are computer-controlled systems that handle the storage and retrieval of goods with high precision and speed. They can significantly increase warehouse efficiency and productivity by reducing manual labor and optimizing space usage.
Materials Handling’s Objectives:
The primary goal is to decrease the number of handlings and the overall expenses of material handling equipment and lower the distances over which the commodities are handled.
The main goal of employing a material handling system is to ensure that the correct amount of stuff is delivered safely, and on schedule.
Also for the least amount of money possible. Materials handling can increase output at reduced production costs, enhance the working environment, and increase material mobility safety. It can improve the use of storage spaces resulting in increased storage capacity.
The Importance of Materials Handling:
- Any successful warehouse must have a practical material handle. So proper materials handling policy will reduce accidents and increase facility productivity.
- Material handling may enhance customer service by making things simple to locate, move, and ship.
also, it can decrease costs by shortening the time it takes to move products and minimizing production damage by managing your products with care. - Employee stress and effort reduced the proper lifting, moving, and storage of equipment, which will also help to decrease injuries in your warehouse.
- Using suitable materials handling equipment and tools, you may manage your goods and materials to have fewer missing items in your warehouses.
- Not only but also removing goods from your warehouse will go more quickly.
It boosts efficiency by saving you time and money. - Materials must be handled carefully at every stage of the supply chain to ensure they arrive in good condition.
A material handling system should include installation to maximize the transportation of goods and materials around manufacturing and storage facilities. - A well-designed material handling system can enhance customer care while. also lowering expenses and decreasing the risk of accidents and damage.
With a material handling system in place, products will be more accessible to identify orders filed more correctly, and worker accidents and injuries will reduce - Your warehouse might become more organized if the goods are appropriately handled. So Finding things will be easier, reducing service time. You can save money by delivering goods on schedule and improving customer satisfaction.
Material Handling Benefits:
An efficient material handling system lets your business have the required inventory in smaller spaces. decreasing time spent on internal tasks (like transport and picking) when possible.
Also, Handling inventory in real time lowers operational costs. Also, material handling improves the flow of products throughout your facility.
Materials are handled carefully at every stage of the supply chain to ensure they arrive in good condition. Loading and unloading trucks. putting individual things on pallets to construct unit loads. and collecting products from shelves to ship out are all part of it.
- Increases Efficiency and Productivity. Also, Assisting your personnel with goods transport, location, picking, and material handling equipment enables them to be more proficient and effective in other jobs.
- You’ll Save Money. Spend on high-quality solutions and train your staff on proper equipment maintenance to avoid paying more for equipment damage.
How Material Handling Can Transform Your Operations and Improve Efficiency
Material handling solutions help to ensure that productivity, safety, and efficiency are the top objectives in a production warehouse setting. These solutions are structures and equipment that help in the organization of space. That can frequently feel unorganized and busy.
These instruments can help move and manage materials in the warehouse and ensure that essential materials are visible to personnel who need them.
To reduce employee efforts, some materials handling solutions aim to lessen physical stress on employees. Conveyor belts. for example, can aid in developing a manufacturing line by transporting products from one spot to another without forcing personnel to hurry back and forth constantly.
Wheels are another material handling device that allows employees to move something previously stationary. These solutions also improve safety, which means fewer employee injuries.
Optimizing Space material handle space on the manufacturing floor is critical for the mobility of personnel, products, and equipment. also, stackable frames and other storage and handling equipment save space on the manufacturing floor by storing non-transporting products.
As a result, storage space reducing and manufacturing floor space increases productivity, and as a result, reducing storage space and manufacturing floor space productivity increases.
Lower Product Damage Manual movement of materials or products across the facility floor may result in product damage if not managed appropriately.
material handling equipment conveyor:
Conveyor systems are a vital component of material handling equipment, offering efficient and automated transportation of goods within various industries. These systems consist of belts, rollers, or chains that move items along a designated path, facilitating the smooth flow of materials. Here are some key points highlighting the significance of conveyor systems in material handling:
- Increased Efficiency: Conveyor systems automate the movement of goods, eliminating the need for manual handling or transportation. With continuous and controlled material flow, conveyor systems enable high-speed and consistent product transfer, significantly improving operational efficiency and throughput.
- Versatile Applications: Conveyor systems are highly adaptable and can handle a wide range of products, including loose items, packaged goods, and bulk materials. They can be customized with specific features such as inclines, declines, curves, or diverters to accommodate varying product types, shapes, and sizes.
- Improved Safety: Conveyor systems incorporate safety features to protect workers and prevent accidents. Emergency stop buttons, safety guards, and sensors ensure the equipment halts in case of any obstruction or danger, reducing the risk of injuries and enhancing workplace safety.
- Space Optimization: Conveyor systems optimize space utilization by utilizing vertical and horizontal areas effectively. They can be integrated with mezzanine floors, vertical lifts, or overhead conveyors to transport materials across different levels, maximizing storage capacity and overall facility layout efficiency.
Guidelines to Simplify Your Material Handling Processes:
- To develop a safer and more effective materials handle system, researchers and industry experts at the Material Handle Institute published a document with the principles of the material handle.
- Plan your material handle system clearly from the start.
- Standardization also attains predictable results while considering flexibility And the standard of your equipment and process.
- Effort Use equipment that will cut down on or eliminate repeated jobs to reduce unnecessary work.
- Unit load to save time and effort in the warehouse. Employ unit loads like containers and pallets.
- Space Utilization arranges your warehouse to make the most of the currently available space. Removing clutter from warehouse aisles and stacking inventory to maximize vertical height. And assembling products from the same category, you can make sure your warehouse organizes
- The system integrates tracking tools to enable prompt material and product verification at every system level.
- The environment uses equipment that will cut down on energy use and stop the release of greenhouse gases. For instance, using an electric forklift instead of a fuel-powered truck is more environmentally friendly.
Best Practices for Material Handling Safety and Efficiency:
Implementing the following best practices can help improve safety and efficiency in your warehouse’s material handling processes:
- Employee Training: Ensure that all employees receive proper training on material handling equipment operation, safety protocols, and warehouse procedures. Regular refresher courses and ongoing training can help maintain a high level of safety and efficiency.
- Preventative Maintenance: Schedule regular maintenance and inspections for all material handling equipment to minimize downtime. and prevent accidents caused by equipment malfunction.
- Ergonomics: Design workstations and select equipment that promotes ergonomic handling, reducing the risk of injuries and improving employee productivity.
- Warehouse Layout: Optimize your warehouse layout by strategically placing high-demand items near the shipping area and organizing aisles for efficient material flow.
- Inventory Management: Implement an effective inventory management system, such as just-in-time (JIT) or first-in, first-out (FIFO). to ensure efficient handling and storage of goods.
- Safety Policies: Develop and enforce clear safety policies, including guidelines for equipment operation, proper lifting techniques, and emergency procedures.
Conclusions
Efficient material handling is critical to the success of any manufacturing or distribution operation. By implementing the right equipment. training your staff. and embracing automation.
you can optimize your material handling processes and improve productivity, reduce costs, and enhance workplace safety.